Our approach
Safety is the first of Downer’s four Pillars. Our steadfast commitment to safety was validated by the materiality assessment Downer undertook this year, which rated ‘Health, safety and wellbeing of our people’ as our number one material issue.
Downer has consistently achieved strong health and safety results in sectors that are exposed to high-risk activities. While we are proud of our safety performance, we also understand we face challenges to maintain and improve this record, and continuously engage with our people to safeguard against complacency in the workforce.
Our commitment to the health and safety of our people and our communities is expressed in strong safety leadership, engagement with our workforce and stakeholders, and a continual focus on identifying and managing risks.
This commitment is reflected in the results we have achieved and our increased presence as Zero Harm thought leaders. Downer’s health and safety commitments are outlined in our Health and Safety Policy, which can be found on the Downer website.
In FY19, Downer committed to achieving the following health and safety targets and objectives:
- Maintain and improve safety results. Downer set a target of zero work-related fatalities, maintaining a Lost Time Injury Frequency Rate (LTIFR) <0.9, and maintaining a Total Recordable Injury Frequency Rate (TRIFR) <4.0
- Increase presence as Zero Harm thought leaders through industry collaboration and consultation
- Unify Zero Harm management systems
- Enhance Critical Risk program and integrate into Hawkins and Spotless
- Improve safety leadership programs
- Increase awareness and support programs to promote the wellness and health of our workers.
The performance information in this section includes Downer, its contractors and Downer employees involved in unincorporated joint ventures in the following business lines: Transport and lnfrastructure; Mining, Energy and Industrial; and New Zealand, but excludes Spotless and Hawkins.
Our performance
TRIFR and LTIFR
Downer’s Total Recordable Injury Frequency Rate (TRIFR) improved from 3.27 in FY18 to 2.70 in FY19. Downer’s Lost Time Injury Frequency Rate (LTIFR) remained below target at 0.57, which is also an improvement from 0.78 in FY18. There were no fatal incidents known to arise from our operations this year, however, sadly in June 2019 one of our Spotless employees died while at work.
Unifying Zero Harm management
Downer took significant steps to further unify our Zero Harm management systems this year. The comprehensive program draws on functional expertise from all parts of the business to identify and share best practice, provide consistency in Zero Harm management, improve mobilisation and flexibility, drive efficiency and increase mobility.
Read more
This process has also provided an opportunity to consistently embed Critical Risk requirements into our investigation, work processes, and learning and development programs. It will also allow for the integration of business management systems and supporting platforms. The program has progressed over the past six months but is expected to take up to two years to complete for all functions.
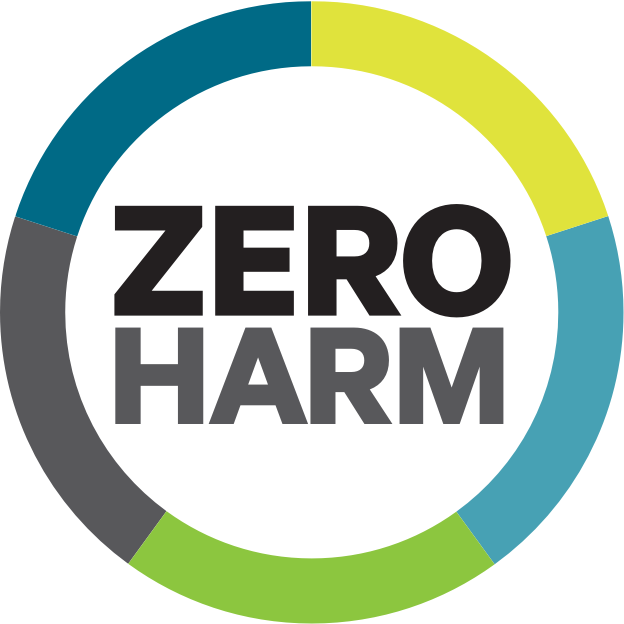
Send in the drones
Critical Risk management program
Downer recorded a 33 per cent reduction in the occurrence of High Potential Incidents from FY18 to FY19. The top 10 Critical Risk activities experiencing a High Potential Incident in FY19 were:
Industry collaboration and consultation
Collaboration and relationship building are important to Downer. We encourage our people to share their knowledge and experience with their industry peers.
Read more
In FY19, Downer employees contributed to a range of industry groups and committees, including:
- Chair of the Safety Managers’ group of the Rail Industry Safety Standards Board, and Office National Rail Safety Data Strategy steering committee and Rail Safety Worker Committee
- Contributor and panel member for the revision of the Occupational Health and Safety Book of Knowledge (BoK) chapter regarding electricity. The BoK is the collective knowledge shared by Australian Generalist OHS Professionals
- Participation and representation on the Minerals Council of Australia Safety and Sustainability Committee
- Contributors and members of the Queensland Resources Council, and several sub-committees of the Council
- Presenting, facilitating and representing our industry at the Safety Institute Australia Young Safety Professionals body
- Participation in the Oil and Gas Queensland ‘Safer Together’ forum
- Signatory to the Construction Sector Accord NZ, a shared agreement between Government and Industry to transform the construction sector
- Board member of Construction Health and Safety NZ, an industry body covering the NZ Construction sector and includes the Regulator
- Board Member of the Green Building Council New Zealand, a non-profit membership organisation that promotes better buildings
- Regular participation in Zero Harm, industry and business group forums, and industry-related university studies.
Spotless suspends risk
Integrating Critical Risk program
Downer has implemented our risk and safety management systems and Cardinal Rules into the Hawkins and Spotless businesses. Incident reporting and injury classifications have been implemented, resulting in the ability to apply consistent data analysis tools and performance monitoring to these businesses. Critical Risk training and workshops have also taken place with Hawkins and Spotless, while incentive targets regarding the implementation of the program have helped integrate it into these businesses.
Improving safety leadership training programs
Key health and safety leadership training programs have been reviewed to incorporate adult learning techniques and experience-based situational training. Where practical, new technology has also been utilised to improve the attendee experience, engagement and learning outcomes. These improvements are consistent with our commitment to our people and are expected to enhance Zero Harm skills and leadership in the business.
Wellness in the workplace
Downer realises our people are our number one asset, and that their wellness has a significant impact on their ability to thrive at work, which in turn affects the success of our business. Injury prevention remains a critical part of improving worker wellness.
Downer CAREs
Our future focus
Downer recognises that the volume of infrastructure projects across Australia and New Zealand presents both opportunities and challenges.
Significant projects put pressure on recruiting and retaining experienced personnel who share our commitment to Zero Harm, which can impact health and safety management.
Downer’s response to this challenge is to continue to harmonise our management of Zero Harm, improve our leadership capability, strengthen the impact of our Zero Harm culture, and maintain our strong reporting culture.
Therefore, future areas of focus for health and safety will consist of:
- Continuing the consolidation of Critical Risk analysis to drive consistent management of Critical Risks in the business. This work will involve detailed analysis of the bowties and critical controls applied across the business for the next agreed risks, other than the five prioritised this year, with a view to harmonise the way those risks are controlled
- Continuing the harmonisation of best practice and management system integration, and adoption throughout the business. This will reduce the duplication of systems and processes across Divisions and drive consistency in the performance and management of those processes
- Building on the expansion of the Mental Health First Aid program throughout the business by increasing the number of employees trained to provide assistance and advancing the education of our workforce around responding to mental health factors
- Championing of the Critical Risk program by executive management to drive cultural enhancement of the program, through the Critical Risk analysis work and the engagement of executives to drive the control performance of their designated Critical Risk
- Improving the use and reporting of lead indicators in the business. Encouraging businesses to deploy relevant and informative lead indicators in areas they have identified as priorities
- Identifying opportunities to improve the functionality and integration technology of our Zero Harm information management systems, through the introduction of a new document management platform and our harmonised information, which will assist in maintaining and mobilising our people.
Emerging issues and market trends
Mental health: The mental wellbeing of staff is an emerging issue, not only for Downer but for our industry peers as well. It is estimated that one in six working age people will be affected by mental illness, and one-sixth of the population will have symptoms associated with mental ill-health.
The Black Dog Institute has estimated that Australian businesses lose approximately $11 billion dollars per year through lost work performance or turnover. Research indicates that a person’s work can be beneficial for mental health, but alternatively can also be a source of mental ill-health. Having a workplace that supports positive mental health and changing the conversation and stigma around mental health is important.
Further, some of Downer’s operations require a fly-in fly-out (FIFO) workforce. Research shows this group is at a higher risk of experiencing mental health issues. In December 2018, a Government-funded Curtin University study reported that 33 per cent of FIFO workers experience high or very high levels of psychological distress. Downer has taken a number of steps to support our FIFO workforce, including the development of a Health and Wellbeing booklet and accompanying pocket guide, which provides a range of information and advice to support the wellbeing of our employees and their families. These resources are available to all Downer employees but have a particular focus on FIFO work.
While we have implemented a range of programs to support the mental health of our operational workforce, we are also aware of mental health risks for office-based staff.
Downer’s holistic company-wide mental health and wellbeing strategy is in place to address this and support our workforce. We have a strong emphasis on training, providing regular courses for mental health first aid, mental health awareness and resilience training. We also provide an Employee Assistance Program for employees and their families.
New technology: Technology is increasingly having an impact on workplace safety. From personal protective devices with sensors that monitor alertness, detect entry into identified zones or warn when equipment is approaching, to applications that support workers in remote areas or who work alone and provide them access to medical assistance. The rise of technology in worker safety requires businesses to remain vigilant to changes in technology, and to assess the opportunity and the risk that these technologies may have in changing workplaces. Downer embraces leading-edge technology to help keep our people safe from harm.