Our approach
Safety is the first of Downer’s four Pillars and Zero Harm is embedded in our DNA.
Our steadfast commitment to the safety of our people is repeatedly authenticated by responses to employee engagement surveys and materiality assessment surveys, as well as by the performance benchmarking we undertake every year.
Downer has consistently achieved strong health and safety results, including in sectors that are exposed to high-risk activities. We are proud of our safety performance, but we also understand we face challenges to maintain and improve this record, and continuously engage with our people to safeguard against complacency in the workforce.
Our commitment to the health and safety of our people and our communities is expressed in strong safety leadership, engagement with our workforce and stakeholders, and a continual focus on identifying and managing risks.
This commitment is reflected in the results we have achieved and our increased presence as Zero Harm thought leaders. Downer’s health and safety commitments are outlined in our Health and Safety Policy, which can be found on the Downer website.
Our performance
Downer committed to achieving the following health and safety targets and objectives in FY20:
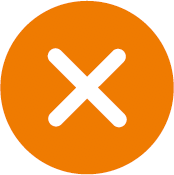
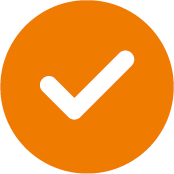
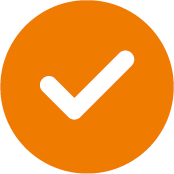
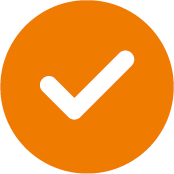
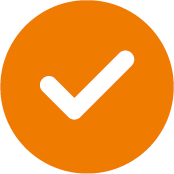
The performance information in this section includes Downer, its contractors and Downer employees involved in unincorporated joint ventures in the following business lines: Australian Operations and New Zealand. Spotless and Hawkins data is reported separately.
In FY20, Downer made strong progress on the implementation of our Zero Harm Strategic Plan. Despite the disruptions of COVID-19, we continued to deliver on the focus areas disclosed in the 2019 Sustainability Report, which are addressed in this section of the report.
Sadly, there was a fatality in our Otraco business in Chile in July 2019. Senior leaders attended the facility to provide support to family and colleagues, and to assist authorities. Consistent with the legal regime in Chile, Otraco received two fines: one of $6,230 AUD from the Labour Authority; and one of $15,575 AUD from the Department of Health. The criminal legal investigation and payment process for the Department of Health fine have been delayed by the impact of COVID-19 on the regulatory authority.
Disappointingly, Downer incurred seven penalty infringement notices for safety breaches, totalling $34,839. This includes the two fines that relate to the Chile fatality. The remaining five consisted of: two fines totalling $7,200 for carrying out
work not in accordance with the Safe Work Method Statement; a fine of $3,000 for carrying out an activity within an unsafe distance of an underground electricity service; a fine of $2,160 for failure to provide access to material safety data sheets concerning disused chemicals on a remote temporary site; and a fine of $674 for failure to comply with a direction issued by an authorised safety officer. We also continue to cooperate with the NSW Coroner and await the outcome of the coronial process to better understand the incident we reported last year concerning the death of a Spotless employee while at work, for reasons which remain unknown.
Downer’s Total Recordable Injury Frequency Rate (TRIFR) for FY20 was below target at 2.88. However, this was an increase from 2.70 in FY19.
Downer’s Lost Time Injury Frequency Rate (LTIFR) also remained below target at 0.67, although it also increased on the FY19 result of 0.57. This is still considerably below industry benchmarks published by Safe Work Australia for all industries which Downer operates in, the lowest of which relates to Architectural, Engineering and Technical Services with an LTIFR benchmark of 1.
Downer Group safety performance (excluding Spotless and Hawkins)

Reading the meter on safety engagement
Critical Risk program
The top five Critical Risk activities for FY19 and FY20 were:
- Working with mobile plant or equipment
- Vehicles and driving
- Working at height
- Falling or dropped objects
- Working on or near rollingstock.
Optimising our Critical Risk program
We understand the nature of the work we do means that the potential for exposure to risks remains present in our workplaces and incidents can continue to occur.
Read more
Downer must continue to evolve our Critical Risk management program, building on its established foundations and optimising the core elements of the program. We will continue to evolve our Critical Risk program over the next year to build on the progress we have already made. The Critical Risk optimisation program will deliver the following benefits into our business:
- Improve the quality of Critical Risk control verification activities
- Reduce duplication and create efficiencies in the verification process
- Further improve Critical Risk knowledge and competence in the business
- Improve data quality and analysis to drive further improvements through the program.
The optimisation program will involve three phases:
- Finalising the consolidation analysis which commenced last year, resulting in consistent understanding and controls in the management of Critical Risks
- Distilling Critical Risk inspection and verification tools to provide tools that are consistent with the consolidated analysis outcomes. This will reduce duplication and the resources required by operational parts of the business to develop and maintain these tools. It will also allow for improvements in the quality of Critical Risk inspection and verification resources, and improvement in qualitative data from these tools
- Refreshing existing Critical Risk training material to reflect the optimised program and deepen Critical Risk knowledge in the business.
Learning to learn
At Downer, we understand the ability to learn is essential to business longevity and resilience. It is also essential to improving Zero Harm performance, which includes the prevention of incidents and injuries that cause harm to people or the environment. This year, we applied the Learning Teams program across the Group following a successful pilot in a selected Business Unit.
A Learning Team utilises a range of experience in the selected activity with a questioning methodology. The team explores each of the key steps in that activity to identify the successes and positives as well as challenges or key actions critical for a successful outcome. The same analytical process is then applied to identify solutions to challenges and improve those key steps or activities. Skilled facilitation keeps the group focused and maintains the open, questioning methodology and avoids the temptation of reverting to known causes or solutions. This process has proven very successful in identifying solutions that may not have been uncovered using other methodologies.
Over the past 12 months, Group Zero Harm has rolled out Learning Teams facilitation training across the Downer Group, increasing the Group’s potential for innovative responses to new and existing challenges in our business.
Communities of Practice
This year, Downer launched its Communities of Practice program. This program harnesses areas of subject expertise within our businesses and utilises that experience in the management of that subject risk or activity. A team of experts for each activity is established to assess relevant information, including incident data as well as Critical Risk and control analysis, and combine this with their own expertise to determine requirements to be adopted across the business.
This work will combine with our Critical Risk program to analyse and understand escalation and control factors and provide Downer with a unified understanding of the risks and safe lifecycle, as well as a benchmark for the safe execution for each activity. All outcomes will also be incorporated into our management system.
Current Communities of Practice include cranes and lifting, traffic management, excavation, trenching and ground disturbance.
Industry collaboration and consultation
Collaboration and relationship building continues to be a focus for Downer. We encourage our people to share their knowledge and experience with their industry peers.
Read more
In FY20, Downer employees contributed to a range of industry groups and committees, including:
- Downer is part of the Logan Water Partnership, which was runner-up for the Water Industry Safety Excellence Award 2020, and placed in the top four for papers presented at the OzWater20 online conference
- Downer’s Skilltech business hosted and facilitated a safety forum that was attended by the majority of their customers. The topics that were covered included lone worker safety, dog safety, communication and the future of safety in the Utilities sector
- The Vic Pipelines business conducted a discovery process with City West Water to explore the presence of unexpected electricity in water meters. The customer participated in learning teams and work insights and was an active part of the discovery process. Following this work, the customer provided positive feedback about the direction of safety within Downer
- Downer’s Learning Teams program was runner-up in the Australian Health and Safety Institute Enterprise Safety Program Initiative Award
- Contribution to the OHS Body of Knowledge (OHS BoK) on behalf of the Australian Institute of Health and Safety (AIHS)
- Collaboration with Risk Management Institute of Australasia (RMIA)
- Collaboration with the University of Queensland (UQ) Risk: Critical Risk Control Master Practitioners, a collaborative research group to improve the performance of hazardous industries
- Participation in the Queensland Generators Safety Forum (QGSR) for the Power Generation Industry
- Collaboration with Safer Together, a not-for-profit member-led organisation for the oil and gas exploration and production industry, which is committed to a strong and consistent safety culture
- Facilitation and attendance at Major Road Projects Victoria conferences and industry forums
- Collaboration with the Office of the National Rail Safety Regulator
- Representatives from our Rollingstock Services (RSS) business participated the International Railway Safety Council Conference
- Our RSS business participated in the Office of the National Rail Safety Regulator review into revised rail safety worker guidelines and is an active participant in the Office of the National Rail Safety Regulator CEO Industry Reference Group
- RSS business holds an active membership with the Rail Industry Safety & Standards Board.
Fusing our functional processes
In Downer’s 2019 Sustainability Report we advised of the initial steps taken to unify the way we manage and perform our work.
Read more
Downer is currently undertaking a long-term transformative program, called The Downer Standard, to align functional processes and policies and unify the way we operate. This will improve efficiency, reduce cost, increase the transferability of our people across the business, and provide a consistent experience for all Downer stakeholders. In time, this work will lead to further cost advantages by reducing the number of separate certifications held by the business.
Over the past year, Downer continued to advance the work to align processes across all functional streams of our business including Zero Harm, Project and Delivery Management, Human Resources, Legal, Finance, Opportunity and Risk, and Procurement. Work was also done to align these processes across our operational Business Units, allowing for any necessary adjustments to legislative requirements.
The work done to reach this alignment also allowed us to examine how we manage and perform a process, and review management systems to identify best practice then implement that across all operational areas of the business.
For Downer’s Zero Harm function, some of the key improvements identified and established have been: stronger collaboration within functions and between functions; identification, sharing and capturing of good practices in the business; a focus on improving project preparation; the elimination of duplicate content; and opportunities for improvement in our documented systems for work.
These aligned processes were developed following strong collaboration between operational and functional areas of the business. This collaborative process helped establish networks and trusted relationships across the business, which continue to provide benefit in the development of Communities of Practice and optimisation of our Critical Risk program, and were particularly useful in our response to COVID-19.
Wellness in the workplace
Our people are our number one asset, and we understand that their wellness has a significant impact on their ability to thrive at work, which in turn affects the success of our business. We support the physical wellness of our workforce through a range of programs and initiatives.
Empowering our people to support their peers
Our Health and Safety response to COVID-19
The COVID-19 pandemic required Downer to make swift changes to how we work in both Australia and New Zealand, and to put systems in place to protect our people, our business and the communities in which we operate, from the virus.
Our response needed to be flexible, current and relevant to our diverse business operations. The impact of the pandemic varied across the business, with some of our people working in higher-risk environments such as hospitals, schools and nursing homes.
Downer’s Group Zero Harm team monitored the emergence of COVID-19 from January 2020, working with the Major Projects business to identify early learnings from the workforce with our China-based joint venture partner, CRRC Changchun, which Downer partners with to deliver Sydney’s Waratah trains and Melbourne’s High Capacity Metro Trains.
Specific information relating to COVID-19 and the management of its risk was distributed to the business. Information bulletins were also regularly circulated to the Downer workforce. From these bulletins, a COVID-19 Management Standard and Pandemic Playbook was developed and regularly updated as our knowledge and experience increased.
Downer’s initial response focused on providing our people with information on the virus to alleviate uncertainty and anxiety, along with guidance on how to restrict the spread of the virus through hand sanitation, social distancing and respiratory etiquette. Central to our messaging was to remind people that if they exhibited symptoms consistent with COVID-19, had been tested, or were a close contact of a positive case, they should not attend work. Concurrently, we worked to identify employees who were at higher risk, as well as those who were overseas, and developed a response to manage the risks to these groups. We quickly restricted, then prohibited, overseas travel, utilising our international travel risk service to provide accurate information and support the return of our people from overseas back to Australia.
We adopted a risk management approach, with a focus on building awareness and verifying compliance with the Critical Controls to prevent and manage COVID-19 exposure in our business.
In addition to our usual workplace cleaning and disinfecting, Downer focused on increasing cleaning of frequently touched or accessed areas, increasing supply and access to hand sanitation and disinfectant, eliminating sharing of kitchenware, and restricting access to our worksites and offices.
In order to support those affected, manage our workforce and understand the impact on our business we introduced a COVID-19 tracker into our existing incident management tool, which enabled us to monitor potential and actual exposures within our business. Collating and having access to this information early was an important part of our response to COVID-19 and helped to keep our people safe and allowed many of our operations to continue under the strict Government restrictions.
As the situation developed, our response evolved to include:
- Staggering of shifts, rosters and meal/rest breaks to allow for social distancing in the workplace
- Changing the layout of meeting and meal/rest rooms to maintain distance between workers
- Redesigning work to minimise the need for working in close proximity with others, and enforcing these social distancing measures
- Minimising high use communal areas and avoiding enclosed spaces
- Enforcing social distancing measures
- Eliminating the use of shared utensils or foods
- Introducing health self-assessments prior to commencing work
- Restricting the number of people allowed in vehicles at any one time
- Increasing cleaning and sanitation of shared tools, vehicles and mobile plant
- Introducing non-contact temperature testing where required
- Directing start-of-shift meetings to occur outside, where possible, to accommodate social distancing requirements
- Increasing random drug and alcohol testing in response to changes to start-of-shift testing arrangements
- Increasing our use of technology for meetings and collaboration to reduce the reliance on face-to-face meetings
- Closing corporate offices and instructing employees to work remotely where possible
- Providing essential workers with documentation to explain their travel and movement during lockdown restrictions
- Increasing our procurement and holdings of disinfectant products, appropriate Personal Protective Equipment and non-contact temperature testing devices
- Producing our own hand sanitiser in New Zealand when procurement of supplies became difficult
- Establishing collaboration platforms for the sharing of best practice resources across the business and accessing mental health information.
Our Victorian workforce was impacted by the second wave of COVID-19. Zero Harm and senior operational leaders responded quickly to manage the situation in accordance with our well-established frameworks, which helped minimise disruption to our permitted workplaces and achieve compliance with all requirements.
The pandemic not only threatens people’s health and economic security, the social distancing restrictions to stop the spread of the virus also left people isolated at a time many needed to lean on others for support. This trio of mental health triggers heightened concern about the welfare of our people. Downer’s Group Health function was crucial in helping to support our people during the pandemic. We provided COVID-19-specific mental health support and increased training in mental health support practices. The team used Microsoft Teams to deliver four 30-minute mental health webinars each week between April and June. The webinars covered important COVID-19 topics including: Talking with children and teens about the pandemic; practical tips on working from home; mindfulness techniques; staying connected socially and creatively; and adjusting to changes at work. The sessions were supplemented by written material that was made available to everyone on the purpose-built COVID-19 information page on Downer’s intranet.
Hundreds of employees tuned in to the webinars each week.
Sanitiser prevails
Our future focus
While the impact of COVID-19 on workplaces will be experienced for some time, the importance of Zero Harm to our people and the communities in which we operate remains an ongoing priority.
Our future areas of focus for health and safety include:
- Optimising the Critical Risk program
- Finalising the harmonisation of best practice and management system integration, as well as the integration of our Critical Risk Optimisation and Centre of Excellence programs into our management system
- Streamlining our analytics and data reporting
- Progressing outcomes of our Communities of Practice program.